Queen’s graduate collaborates with The McAvoy Group on structural design of offsite housing solution
Queen’s University Belfast Civil Engineering graduate Hung Phung Quang is already making an impact on local industry as he joined a team at The McAvoy Group to collaborate on the structural design of a new offsite housing solution.
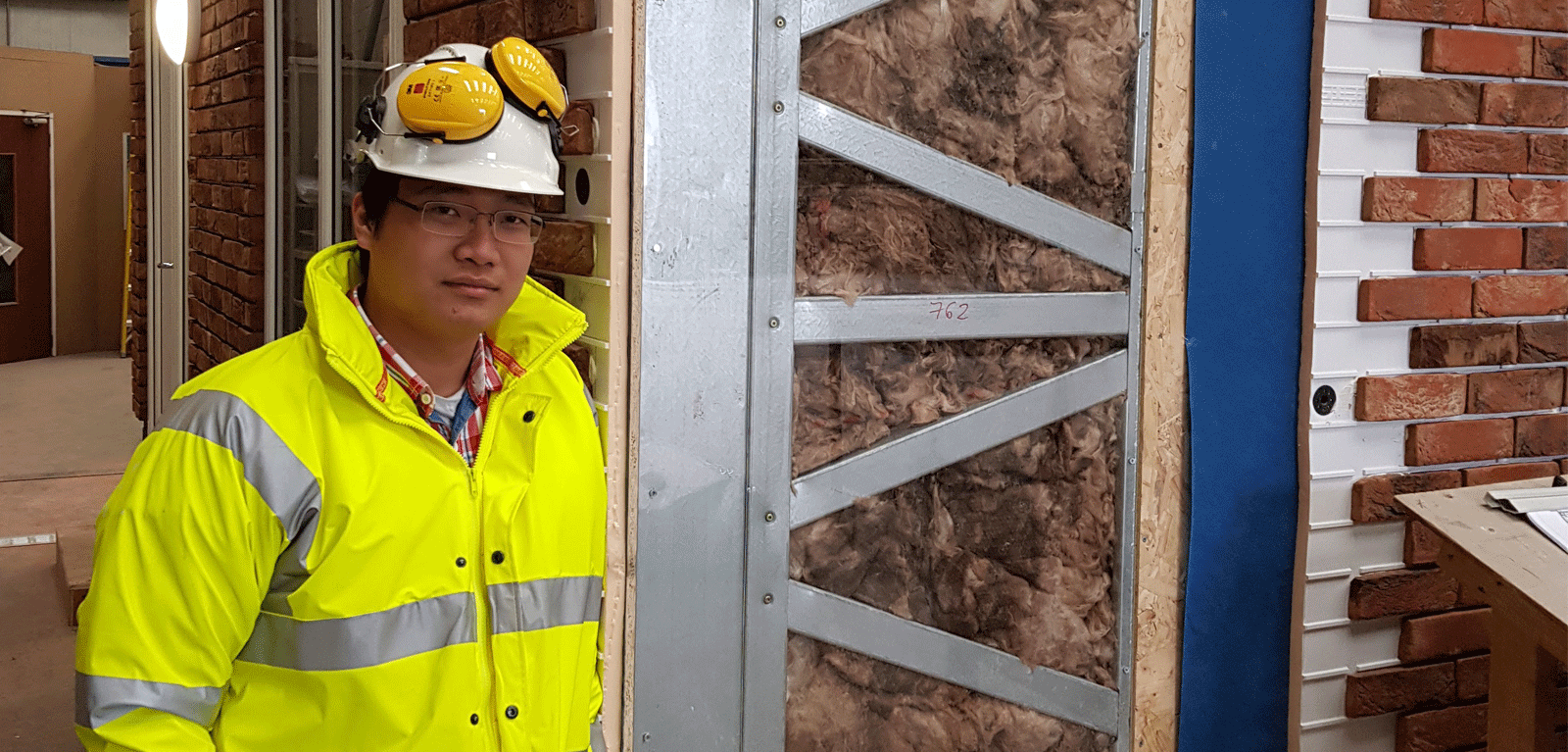
The first application is the first affordable housing scheme to be built offsite in Northern Ireland.
Offsite construction means that elements of a construction project are manufactured in a factory environment before being installed on site.
New homes are built in the McAvoy factory, before being transported to their final location. Apartments and houses manufactured offsite will be installed by McAvoy for a leading housing association in Northern Ireland.
The new offsite housing solution which Hung helped to develop involves the manufacture of houses and apartments to the highest quality standards, internally and externally, before leaving the factory and require minimal assembly on site.
This approach generates significant time and cost savings and the reduction of the overall build programme by up to 60 per cent.
Hung played a key role in the structural design and validation process of the offsite prototype housing solution. The development process was supported by Queen’s University Belfast who carried out material testing. The prototype is now installed at the Group’s factory in Lisburn, Northern Ireland. The innovative development work carried out on the structural design and lifting strategy, using lightweight steel-framed construction, was crucial to the project and underpinned the solution now being applied to live projects.
Commenting on the project, Hung said: “The KTP Project was a great opportunity for me to work between Queen’s lecturers and The McAvoy Group – one of the leading offsite specialists in the UK and Ireland. Their team is incredibly passionate about what they do and delivers projects to extremely high standards.
“I developed my knowledge in both academic research and practice in industry by designing solutions for industry. We used a laboratory to test the design and I worked closely with the McAvoy manufacturing team to bring the solution to market and into production.”
During the design process, Hung worked with Virtual Reality to enable the team to visualise the buildings at a 1:1 scale at an early stage. This resulted in faster appreciation and acceptance of the design.
The application of Augmented Reality enabled the manufacturing team to identify components and systems within the fabric of the building. This allowed the team to refine the design and assembly process digitally, which added further efficiency savings to maximise work offsite
Originally from Vietnam, Hung worked on a collaborative Knowledge Transfer Patnership between Queen’s and McAvoy on a full-time basis for two years. The project was co-funded by Innovate UK and Invest Northern Ireland.
Knowledge Transfer Partnerships are schemes that link up businesses in the UK with academics to work on specific, strategic projects. Invest NI has committed to provide £4.9m in funding between 2018-2023 towards Knowledge Transfer Partnerships for Northern Ireland businesses.
KTPs are mutually beneficial partnerships as businesses are able to bring in new skills and the latest academic thinking which allow them to innovate and grow, and they also give academic teams and graduates invaluable industry experience.
Queen’s is the leading institution in the UK for Knowledge Transfer Partnerships.
Following the completion of his KTP, Hung is now employed as a permanent Research Engineer at McAvoy. He is working on the first application of the new offsite housing solution which is an affordable housing scheme in Carrickfergus. The homes that he helped to design are now in production.
David Clark, Head of Manufacturing and Innovation at McAvoy said: “The team at Queen’s worked with us on the project in a collaborative Knowledge Transfer Partnership, providing input on testing and structural design. In return, we were able to give valuable industrial experience and the opportunity for academic research into new methods of construction to address the housing crisis.”
Media
Media inquiries to Jemma Greenlees at Queen’s University Communications Office T; +44 (0)28 9097 3087 E: j.greenlees@qub.ac.uk.