Dimensional Addition
Designers draft and analyse simple conceptual layouts to prove an idea before expending resources on a full-blown 3D finite element analysis model. Once an acceptable solution has been found at the conceptual stage, the original CAD representation may then be re-constructed as a 3D model. A considerable amount of unnecessary duplication of endeavours occurs during this process. Dimensional addition, the reverse process of the more established idea of dimensional reduction , is therefore advocated as an effective saving for the designer, whereby the transition from 1D skeleton to 3D solid at is least semi-automating and so minimising what would otherwise be a tedious and costly drafting stage.
Geometric operations are necessary to generate a coherent solid model from the conceptual layout. Modern CAD systems are highly productive tools for concept embodiment, detailing, and preproduction engineering. Systems with fully integrated behaviour modelling and simulation functionality provide the engineer with tools capable of supporting a number of engineering steps in all life-cycle phases of a product. The simplified operations developed at QUB FEM facilitate rapid and full re-use of idealised conceptual model details to create full solid CAD and analysis models. They provide functionality for adding complexity to simple models are dimensional addition, detail insertion and symmetry addition, all of which have been demonstrated in the examples shown.
The integration of analysis modelling into CAD systems has enormous potential benefits. A huge range of geometry construction and modification tools are available, whilst access to the feature tree used to create the model means that optimisation studies can modify design geometry directly rather than the finite element mesh. Thus analysis-driven design is facilitated.
Geometric operations are necessary to generate a coherent solid model from the conceptual layout. Modern CAD systems are highly productive tools for concept embodiment, detailing, and preproduction engineering. Systems with fully integrated behaviour modelling and simulation functionality provide the engineer with tools capable of supporting a number of engineering steps in all life-cycle phases of a product. The simplified operations developed at QUB FEM facilitate rapid and full re-use of idealised conceptual model details to create full solid CAD and analysis models. They provide functionality for adding complexity to simple models are dimensional addition, detail insertion and symmetry addition, all of which have been demonstrated in the examples shown.
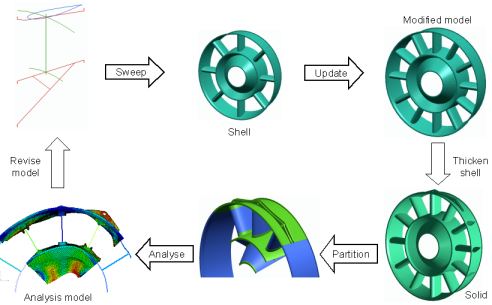
The integration of analysis modelling into CAD systems has enormous potential benefits. A huge range of geometry construction and modification tools are available, whilst access to the feature tree used to create the model means that optimisation studies can modify design geometry directly rather than the finite element mesh. Thus analysis-driven design is facilitated.