Electrothermal Actuators
Electrothermal microactuators operate under the principle of resistive heating, meaning heat is generated in conducting arms which in turn causes expansion and thus deflection from the normal position. The devices normally use DC current which when disconnected causes the arms to cool and return to the normal position. Polysilicon was the material of choice because it is suitable for surface micromachining techniques and doping amounts can easily control its' resistance.
Two designs were found to be the most successful; a hot-cold arm actuator and an opposing hot arms design. The best deflection was measured at 11.9µm for a hot-cold arm design, with an input power of 39mW. The opposing beams design achieved a deflection of 10.9µm with an input power of 303mW. The deflection characteristics of both designs were in good agreement with theoretical model.
Hot-Cold Arm
(by Gary O'Neill - MEng. Student 2003 and Richard Parke - MEng. Student 2004)
The actuator design is based on the bimorph effect, which relies on the difference in thermal expansion of variable microstructure sections. A narrow arm (‘hot’arm) is positioned parallel to a wider section (‘cold’arm). The electrical resistance of the‘hot’arm is higher than the‘cold’arm, so when electric current passes through the actuator, the‘hot’arm is heated to a higher temperature. The‘hot’arm expansion causes the tip of the device to rotate about a flexure element.
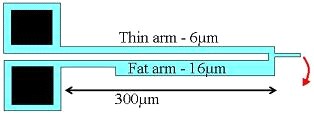
Opposing Arm
(by Richard Parke - MEng. Student 2004)
The one hot arm model as used in the conventional design is an effective method of actuation but the direction of displacement is limited. A double hot arm model is capable of larger deflection and force and it is much more adaptable. The double hot arm is simply a loop of polysilicon material with no variation in the width so the whole structure expands equally.
The expanding effect of the double arms can be utilised in a simple mechanical system to produce a very effective actuator. If two double hot arm systems are used in an opposing direction a connector beam will create a turning force. The turning force thus operates a centre arm. This actuator has the potential to produce quite large displacements and the only draw back being the space required.
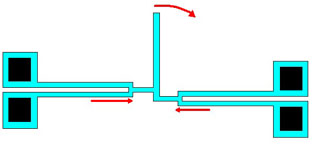