Research Impact
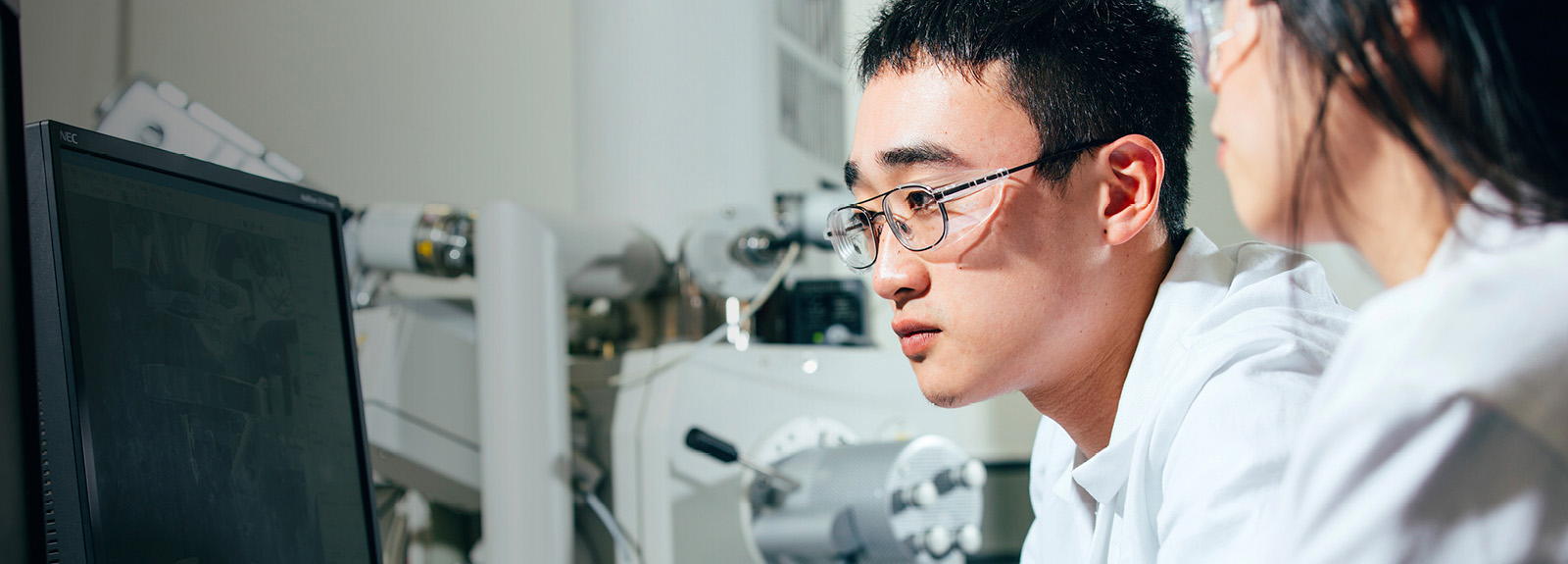
The depth and breadth of our research impact is exemplified by the case studies below, which illustrate how we strive to commercialise our work, often via collaboration with industrial partners, in order to ensure maximum reach and benefit.
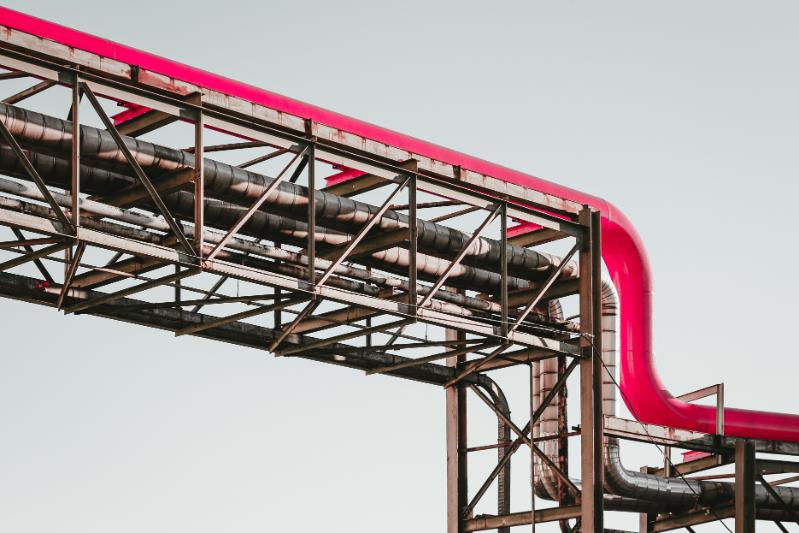
The QUILL research centre within the School of Chemistry and Chemical Engineering was the first research centre to focus on the development of ionic liquids (liquid salts) and their applications in green chemistry. It carries out fundamental studies on the design and performance of ionic liquids, as well as their application in industrial processes.
The centre has a strong background in understanding structure-property relationships in ionic liquids from a fundamental perspective which forms the basis for controlling and exploiting them. This expertise has allowed entirely new ionic liquid-based approaches to remove mercury from natural gas and condensate supplies to be developed. This is a considerable challenge since it requires complex mixtures of inorganic, organic, and elemental forms of mercury to be extracted from natural gas and liquid hydrocarbon streams on an industrial scale, and must be sufficiently rapid to protect down-stream facilities from spikes in mercury content.
Led by Professors John Holbrey and Ken Seddon from the School, successful on-site commercial pilot testing in collaboration with industrial partners has led to transition to full plant implementation. This was based on data which showed that after 3 years continuous operation of the first full system, the mercury concentrations from the outlet gas stream remained low, the system met all plant specifications and the designed material achieved its design lifetime of up to three times that of previous commercial alternatives (such as sulfur-impregnated activated carbon). This potential long operating lifetime was identified in early stage laboratory screening and was sustained through pilot testing and into full-scale implementation.
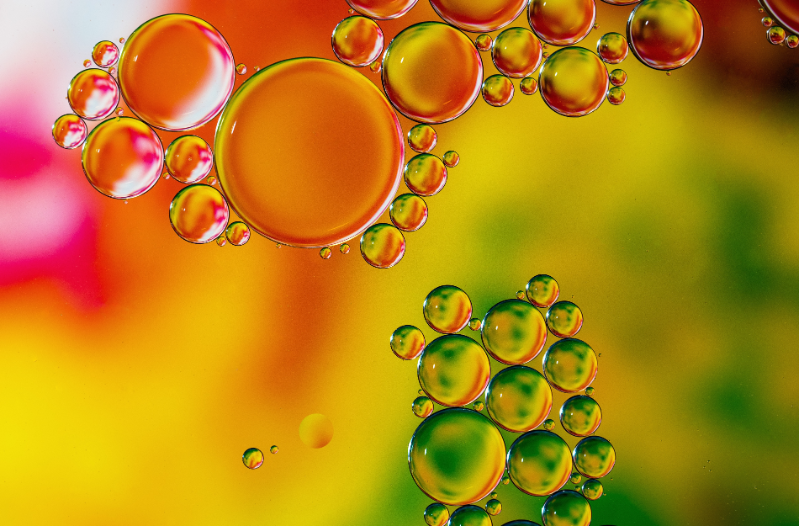
Alkylate gasoline is the cleanest and most efficient gasoline blending component (low emissions, high octane number). As far as fossil fuels go, it is both green and economically attractive, with >500 alkylation plants worldwide. The main drawback of the two established technologies for alkylate gasoline production are the catalysts they use: hydrofluoric acid (HF) and sulfuric acid (H2SO4). HF is a poisonous liquid with very high vapor pressure, easy to recycle but requiring multiple costly handling precautions. H2SO4 is a non-volatile liquid, but its recycling is an energy-demanding, large-scale operation producing significant waste streams.
The QUILL research centre within the School of Chemistry and Chemical Engineering has provided long-term research expertise and support for Chevron’s development of ISOALKYTM Technology, replacing the conventional catalyst for the production of alkylate gasoline, hydrofluoric acid (HF), with an ionic liquid. HF is an extremely corrosive and poisonous volatile liquid, making the safe plant operation demanding and costly. The non-volatile acidic ionic liquid used in ISOALKYTM is inherently safer and easier to contain, making the process cheaper and safer, in addition to yielding high quality fuel. The first full-scale plant (580t per day) is now operating, and the Chevron/Honeywell UOP partnership (the ISOALKY Alliance) has already licensed the technology to other producers.
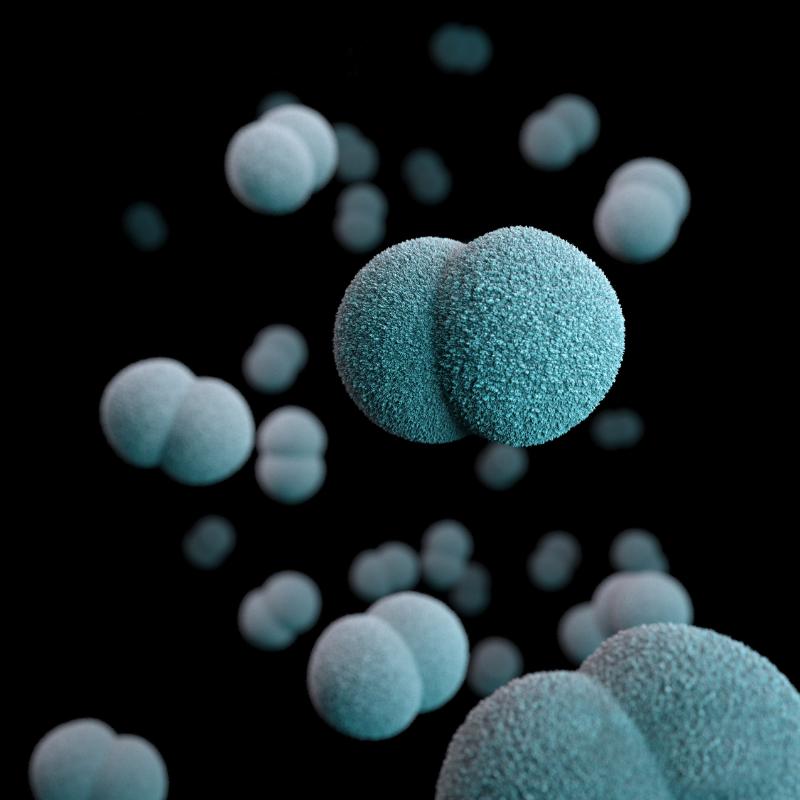
C. difficile (C. diff) infections are a major problem; in 2015-16 in the UK alone, there were 5,200 cases in hospitals and more than 14,000 in primary care institutions. It is estimated that there are more than 1,000,000 cases in the US and Europe each year. This anaerobic bacterium usually affects patients with pneumonia or cancer who have been treated with broad spectrum antibiotics (especially cephalosporins) which have destroyed their natural gut flora. Although there are two drugs (metronidazole and vancomycin) that are currently partially effective, C. diff infections still cause >30,000 deaths annually in the USA and >10,000 in Western Europe each year. The economic cost of C. diff infection is significant, with one study estimating annual acute care costs at USD4,800,000,000 in the USA. New therapies are thus desperately needed.
A series of bis-benzimidazole (BBZ) compounds synthesised by the Mann group within the School of Chemistry and Chemical Engineering at Queen's University, and collaborators, has led to the discovery of Ridinilazole, which is closely related to the original BBZ compounds. Ridinilazole, which has shown considerable promise as a new antibiotic specifically targeting C.diff. is being brought to market by Summit Therapeutics
In Phase 2 clinical trials (2014 – 2016), Ridinilazole demonstrated statistical superiority over the current standard-of-care drug vancomycin. The results were so strong that the US Food and Drug Administration has accorded the drug ‘Fast Track (development)’ status and ‘Qualified Infectious Disease Product’ status. In 2017, the US government’s Biomedical Advanced Research and Development Authority awarded Summit Therapeutics a contract worth USD62,000,000 to support the clinical and regulatory development of Ridinilazole. Phase 3 clinical trials are now in progress.